Geotechnical / Structural Monitoring
New York City (NYC), the most populous city in the United States, also has one of the most number of buildings within a given area. By this the NYC Department of Buildings has come up with a building code and accompanying procedures, that are much more stringent than those prescribed under the International Building Code (IBC).
The “Technical Policy and Procedure Notice #10-88 (TPPN 10-88)” requires that any constructions must have a monitoring program to reduce the likelihood of construction damages to existing, adjacent structures and to detect at an early stage the beginnings of damage so that construction procedures can be changed.
TPPN 10-88 has the following major criteria, among others:
Monitoring Mode
a. Vibration Monitoring
b. Structural Movement Monitoring
c. Crack Monitoring
Unit of Measure
PPV = in/sec (mm/sec) or Peak Particle
Inches (in) or millimeter (mm)
Survey Instrument or Total Station
Accuracy of. +0.01ft (3mm)
Inches (in) or millimeter (mm)
Photographic Documentation
Sensitive to 0.001in (0.003mm)
Maximum Permissible
PPV = 0.5 in/sec (13mm/sec)
Seismograph/Triaxial Geophone
¼ in. or 6 mm
¼ in. or 6 mm
Quality Control Laboratories LLC (QCL), has state of the art equipment for all three (3) of these monitoring modes; Vibration, Movement and Crack.
QCL also has Tilt, Water level and Inclinometer Monitors in addition to those already mentioned, but for the purpose of structural health monitoring of adjacent structures to constructions sites this presentation will focus on the three modes under TPPN 10-88.
VIBRATION MONITORING:

Vibration Monitor (sensor is the blue square)
Vibration monitoring is the measurement of passing movements in the ground or in a structure, using a seismograph, geophone or other instruments such as an accelerometer, to detect and record the movement. It is the most commonly-used method for identifying potential vibration damage problems due to construction.
The vibration instrument would be measuring movements in Each of the three directions at right angles to each other (longitudinal or radial, transverse, and vertical). The sensors of these vibration monitors shall be oriented so that the longitudinal phase shall be towards the direction or \source of vibratory movement.
QCL has both manual and remotely operated monitors. Remote Monitors, are automatic and autonomous units which could be programed to measure, start or stop at specified time intervals. These functions could also be remotely controlled from the office. Obtained records ( working hours or 24/7 when required) would be periodically sent to our data base. When trigger points are reached or approached (depends on programming) these remote monitors would immediately and automatically send emails to selected recipients, so that prompt and appropriate actions could be taken.

Survey Prism
STRUCTURAL MOVEMENT MONITORING:
Structural Movement Monitoring shall be the observation and recording of horizontal (deformation) and vertical (settlement) movements of adjacent building. This is accomplished by optical readings of target reflector prisms attached at strategic points on adjacent buildings. The prisms would be shot by highly precise survey instruments called “Total Stations”. The readings from the target prisms are then referenced to at least four (4) prisms installed in places away from the “area of influence” of the construction. In NYC, this may be up to 90 feet radius from the perimeter of the construction site. These readings are then computed in a mean least square method by a special computer program, and their precise coordinates determined. The accuracy of this instrument could be up to ten thousandths of a foot ( + 0.0001 ft).
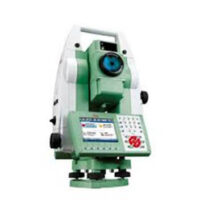
Total Station
For structural movement monitoring we have the manual and automatic total stations. Our manual equipment, as the name implies is carried by able field survey technicians and engineers. Depending on the demands of the project or the contractor, readings are usually taken once a week and more when needed or necessary.
For projects with more demanding standards, and when more frequent readings are needed, we deploy our AMTS, or Automatic Motorized Total Stations, which can read continuously or at pre-programed time intervals. The readings are transmitted in real time to the database or designated recipients. These readings are considered raw data, but for field purposes may be utilized for informed decisions by the Engineer of Record. Formal written or electronic reports could be prepared for submission to designated recipients.
As with the remotely controlled Vibration Monitor, AMTS can also be remotely controlled. Power sources may be from the building where the unit is mounted or from the contractor’s line. In the absence of a viable power source; solar power and back-up batteries could be hooked into our automated systems and make them totally independent.

Tell Tale Crack Monitor
CRACK MONITORING:
Manual Crack Monitoring is the photographic documentations of “tell tales” crack monitoring devices mounted on either side of a crack with a graduated piece that could slide independently, alongside or one on top of the other. Movement is determined by the difference between a baseline photo’s measured gradation and that of a recent picture.
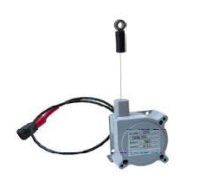
String Potentiometer
Automatic Crack Monitoring employs several different kinds of equipment; QCL uses string potentiometers attached to a wasp. A string potentiometer is a transducer used to detect and measure linear position and velocity using a flexible cable and spring-loaded spool; The cable is stretched over a crack and anchored on one side of the crack while the spool and electronic sensor is on the other. Any stretch or movement is detected and then converted into an electrical signal that translates to a measurable distance, and then transmitted by the wasp to the central database. Though this may be in real time, the gathered data is sent periodically at pre-programmed intervals to the data base. A report is then made based on this received data. Both the potentiometer and the wasp consumes very little energy and therefore can be deployed with very little maintenance in hard to reach areas and may be left in their position for as long as five (5) years.